top of page
On Friday, 22nd of November, we used the opportunity of our partner MWT recycling visiting Berlin to take you behind scenes to bring more clarity around MWT’s mission: What are the added values of their expertise for our industrial clients and partners? What is a regular work day?

Before diving into the discussion let’s reintroduce MWT. Created in 2015, “Maschinenbau und Wertstofftrennung GmbH & Co” (which means Mechanical engineering and material separation) is a state of the art recycling company based in Diepholz, Lower Saxony. Their main mission, as you will read further in the discussion, is to recycle every small piece of industrial scrap and squeeze every grain of raw material in it to reintroduce them on the market.
TQ: Hello Elisabeth, it is very nice to have you here in Berlin! Can you present yourself and your mission?
I am Elisabeth Bröring (ELBR), I worked for a logistics provider for many years in Germany and in Shanghai for three years. I returned in 2016 and I got the opportunity to join MWT, which was a small company then. We have now 15 team members and we focus on recycling raw materials and critical raw materials, like copper, aluminum, and precious metals like silver, gold, and palladium. These metals are not only very valuable but can be recycled almost infinitely.
We work with two main inbound streams: one from other recycling factories and another one from industries. The second one comes from industries such as the automotive or electronics sector that generate waste, faulty batches, unsold parts and damaged goods. We try to help these industries make the most out of their scrap. We aim to recycle heterogenous materials or compounds, especially those that are technically difficult.
From your point of view, what’s to gain for industrial companies working with our consortium?
ELBR: I have the feeling that not only sustainability departments are caring about these topics now. Procurement teams and production departments are starting to reconsider how they manage materials and waste. It’s no longer just about cost savings; it’s also about gaining better data, ensuring compliance, and meeting the growing need for sustainable practices.
Incinerating waste materials often comes with a cost, but hidden within that same pile might be materials of significant value, such as precious metals in discarded motherboards. This is where we come in, helping companies realise they’re throwing away money and showing them how to turn waste into profit.
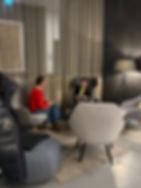
Beyond that, once we [with Terraquota] dismantle the products and analyse the materials (like identifying which types of plastics or cables are used) we give recommendations to product design teams to improve future designs. For instance, if a product has two types of plastic, could it be made with just one? Simplifying designs like this makes recycling easier, especially in industries like automotive, where black plastic is particularly hard to sort.
That said, it’s important to add that even with the best recycling processes, we can not meet global demand for materials like copper through recycling alone. Not even close. Therefore, I don’t think recycling is going to replace mining in the long term, that’s not the point. But it is important to not rely only on mining and reuse the raw material that is already in Europe by extracting it from scrap. It’s helping avoid raw materials shortages and it’s producing way less CO2 emissions. The thing is, there is some growing industry that we have to take into account like AI.
So let’s say an industrial wants to send you their scrap, what are they putting in their containers and isn't complicated logistics-wise?
ELBR: We accept all kinds of production scrap and downstream recycling fractions that contains valuable materials like copper, aluminum, and precious metals. It could be anything from circuit boards to cables or control units from the automotive industry for example. The scrap could come in various forms, like products’ parts, containers, or loose materials. It depends on the company’s needs and how they already handle their waste. What’s most important is that the materials are of the right kind, and they’re packed in a way that makes sense for transportation and processing.
Logistics-wise, it's not complicated at all ! We pick it up so the industry doesn't have to do anything. Most companies want an easy day-to-day operation, and even if there's already one company handling their waste, we don’t want to disrupt that. We can work with the existing partners, like shipping or waste disposal companies. It's a collaborative approach rather than competition.
So what’s your secret? How do you recycle the scrap and what do you produce?
ELBR: The goods arrive at our facility in bulk or in containers, especially when they come from industries, like automotive or electronics. We start by feeding the materials into the production line, where they get shredded into smaller pieces. Then, we use milling to break down the compounds and change their morphology, so we can separate the materials more efficiently. We then sieve and separate the materials by their density. Think of it like sorting rice, coffee beans, and spaghetti in a food industry setting. It’s all about grouping materials of similar size together.
It can sometimes look like a powder, but typically, it's granulated into small, round or egg-shaped particles, about 0,25-10 millimeters in size. The process of milling and sieving is really key to separating out the different materials so we can then work with them more easily. It depends on the engineering requirements, but most of the time, we end up with this granular material.
So is the granulate or powder ready to be reused like that and how does the industry benefit from it?
ELBR: Once we’ve processed the materials, we sell them to the metallurgic industry. The smelters take over from there, doing the final smelting and refining processes. After that, the metals go back into the industry. It’s a very straightforward process with no big marketing or sales efforts required on our end, as we simply go to the smelters who buy the material we produce.
One of our customers actually has a closed-loop system with us. They hold the contract with the smelters, and we provide the materials that go under their contract. It’s a virtual loop, but it’s still very much a closed loop. We like this approach because it really integrates us into the broader recycling chain. Not only is it cutting down transportation costs, it’s an amazing way to introduce the Circular Economy without disrupting the whole supply chain. Concept that is going to be more and more important in the next few years.
Author: Elisabeth Bröring & Emma Dauphin Reviewed by: Irina Chèvre & Hélène Isermeyer
Published: December 2024
Related Posts
bottom of page